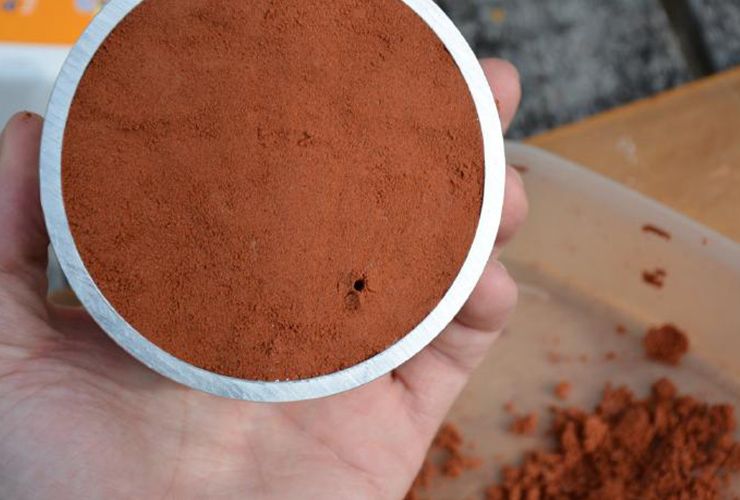
Getting Started With Delft Clay Casting
Delft Clay works a lot like sand casting does, however allows finer details in the cast, and with the aid of a metal flask ring(s) it makes the casting process enjoyable and fairly easy, even for a beginner.
What is Delft Clay?
The Delft Clay method of casting is a form of sand casting. It makes it possible to make remarkably sharp castings of many objects in gold, silver, and other metals. After casting, the Delft clay can be re-used immediately.
Cast objects are very detailed and hardly distinguishable from the original model after the casting, the clay 1 mm around the cast is burned and has to be removed. The rest of the clay can be re-used immediately.
Where to get Delft Clay?
How to Use Delft Clay?
We suggest watching our recommended videos below and checking out the Delft Clay handout below from the official website.
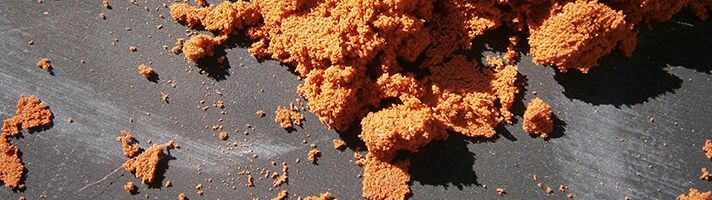
Online eBook: How do I cast with Delft Clay?
Download: 05-hand-out-delftclay.pdf
Casting with Delft Clay is almost the same as sand casting if you know what that is if not have a look at this manual how-to guide (.pdf)
Basic Tutorial: Â Casting with Delft Clay & Pewter.
Just to show you how easy it is, this is my first-ever attempt at any kind of casting.
I choose to use pewter due to its low melting point and ease of casting, Pewter flows into the mold very easily compared to metals with higher MP and because doesn't burn the clay, With higher melting points, the mold has to be heated and the available pour time is very unforgiving. Â
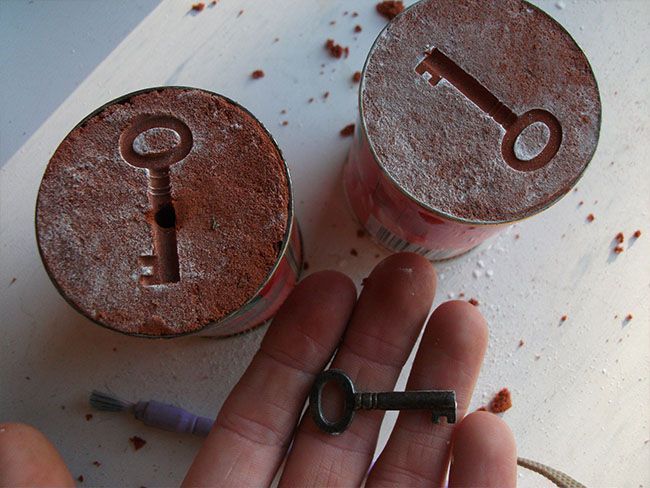
I used:
- Delft Clay or Petrobond Sand could be used.
- An unwanted pewter mug (for the metal)
- An old key
- A small tomato tin can (as I didn't have the casting ring/flash at hand)
- Talcum powder or any releasing agent suitable for casting and high heat.
- Butane torch/heat source.
- A Crucible, A Ceramic flower pot, or an Iron pan would do.
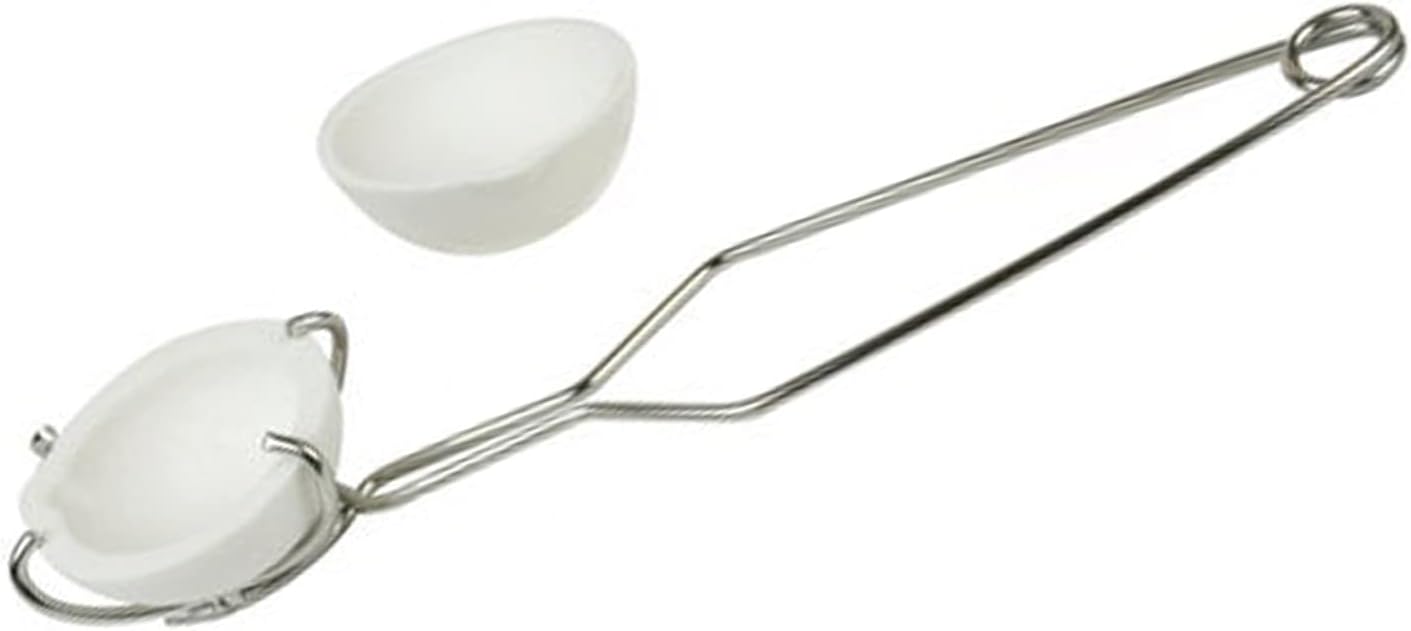
Ceramic Crucible
Good thermal stability, high strength, shock resistance and long-lasting.
Prepare Your Workspace
Set up a well-ventilated and organized workspace. Ensure you have proper safety equipment, including safety glasses and heat-resistant gloves, as working with a blowtorch and molten metal can be hazardous. Place all your tools within easy reach for a smoother workflow.
Getting Started
It took approximately 12 minutes, which included the casting process. Honestly, I'm amazed at how straightforward it was! What's more, I managed to complete the task using just two small, old cans to contain the clay, leaving plenty of room for even greater improvements!
Create a Simple DIY Casting Flask
I did this by cutting in half a used tin, A tin will do and is fine for casting Pewter just be careful not to get molten metal on the paint of the can as it will produce unpleasant toxic fumes.
Mold Preparations
Pack the tin (DIY Casting Flask) halves tightly with Delft Clay.
Lightly dust the blank molds with talcum powder to facilitate the separation of the key and molds. Press one half of the key into the center of the clay mold and place the other half on top, ensuring a firm connection.
Mark reference lines on both halves of the mold for re-centering during casting.
Gently separate the molds and remove the key, leaving a negative mold on both sides.
Create a pour hole in the center of the negative mold using a skewer and fashion a funnel on the opposite side with a knife, adjusting it as necessary.
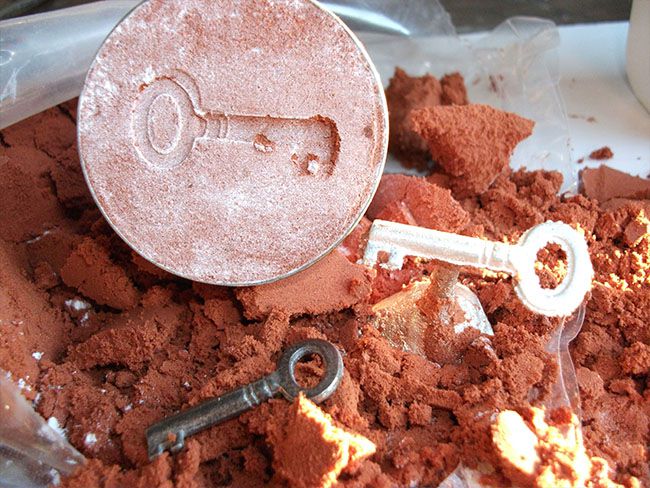
Next, assemble the mold, ensuring that the center marks align. Place it carefully on the table with the pour hole facing upward.
Melt and Cast
With safety gear in place, melt the pewter in the crucible. While maintaining heat, gently shift the crucible toward the mold and execute a swift, controlled wrist action to pour the molten metal. Wait for it to cool.
With my First Attempt: The key poured flawlessly, even without the need for an air hole.
However, some filing will be necessary. The closer the alignment and match of the two molds, the less filing work is required.
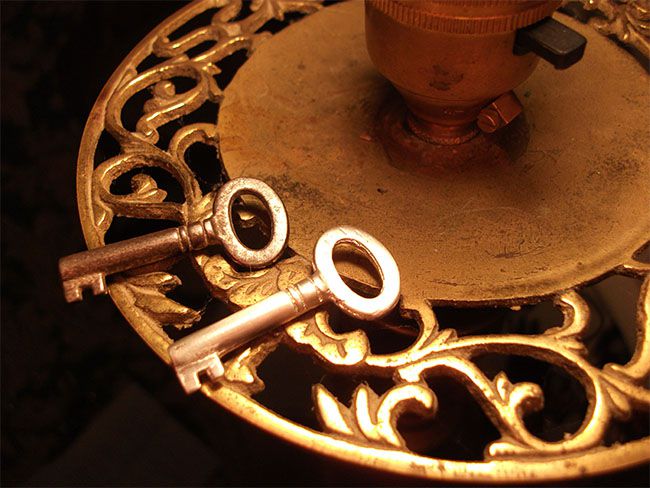
For more detailed instructions on how to use Delft Clay refer to this article: How To Cast With Delft Clay and watch the video below.
Here are some examples of delft clay castings to inspire you!
Below are some examples of people work casting with Delft Clay from all over the world, hover over the image to see a short description and click on the image(s) to see the image website source and more about the artists involved as you can see delft clay is being used for making bits of knives, steampunk like sculptures, rings. Whatever you can imagine.
The finesse of the clay keeps so much detail from the cast! even picking up a bit of nature and casting them in silver makes beautiful pieces!
- silver cast from fluxstudios.
- small eyes enormous things.
- cameo ring by rubygirl jewelry
- silver acorns by lovelydeer
- hans meevis
- casting silver bolsters britishblades
- casting buttons for bangles laurajanebouton.
- lego ring rubygirl jewelry
Delft Clay's Story
The Delft Clay Method of Casting consists of a mold and moldable Delft clay, in which objects can be cast remarkably sharp and fast. The Delft Clay is reusable and cannot dry out due to its special composition.
Great little video series on casting with silver!
Part one: Setting up the flask, adding the Delft clay, and the shape of the cast.
Part Two: Melting the silver, pouring it into the delft clay mold, and removing the casted result (doesn't include finishing, sadly.)
Delft Clay casting offers a rewarding and creative outlet for those interested in crafting metal objects.
As a beginner, follow these steps and practice to refine your skills. With time and experience, you'll be able to create intricate jewelry and custom metal pieces that reflect your unique style and creativity.