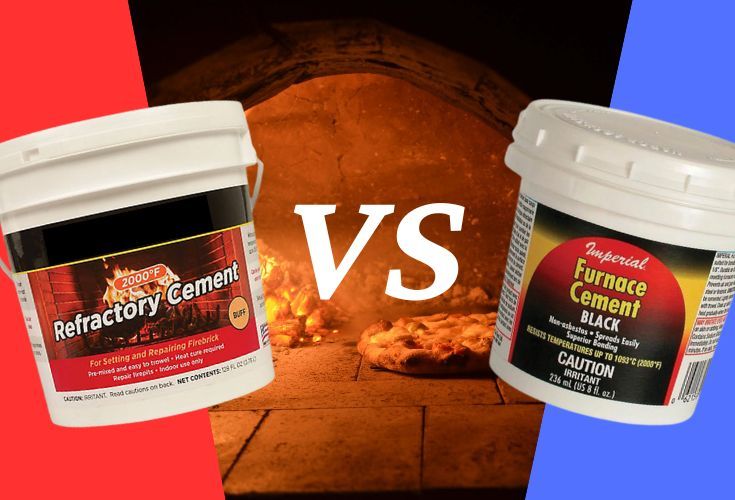
Furnace Cement vs Refractory cement - What do I need to use?
Furnace and refractory cement are two essential materials used in high-temperature applications, such as furnaces, kilns, and fireplaces.
While both cements are designed to withstand high temperatures, they differ in composition, durability, and application methods.
Understanding the differences between these two cements is crucial when choosing the right material for your project.
In this article, we will explore the differences between furnace cement and refractory cement, their uses and applications, advantages, and disadvantages, and provide tips for choosing the right cement for your project.
By the end of this article, you will have a better understanding of these two cements and be able to make an informed decision for your next high-temperature project.
What is Furnace Cement?
Furnace cement is a type of cement that is designed to withstand high temperatures, typically up to 3000°F.
It is composed of various materials such as silica, alumina, and calcium aluminate, which are mixed with water to form a paste-like consistency. This cement is used in a variety of applications, including sealing and repairing furnaces, fireplaces, and boilers.
One of the primary advantages of furnace cement is its ease of use. It can be applied with a trowel or putty knife and can be shaped to fit any surface. Furnace cement is also relatively inexpensive compared to other high-temperature cements, making it a popular choice for DIY projects.
However, furnace cement also has its disadvantages. It is not as durable as other high-temperature cements, and it can crack and break down over time due to exposure to heat and moisture. Furnace cement is also not suitable for use in applications where it will be exposed to direct flame or extreme temperatures.
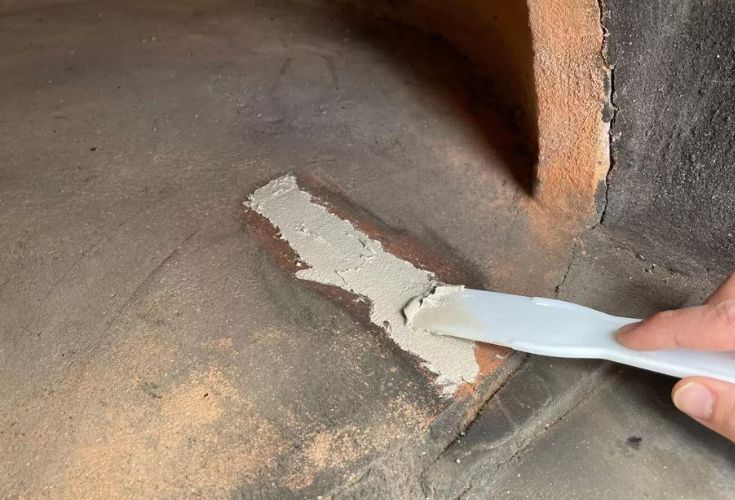
Some common brands of furnace cement include Rutland Furnace Cement, Quikrete Furnace Cement, DAP High Heat Mortar and despite it's amazing slogan "Iron will melt where this cement will stand" avoid Pecora Asbestos Furnace Cement and any other cement containing harmful substances, if you can even find them that is...!
Pecora #Asbestos Furnace Cement. Bekend onder de slogan: "Iron Will Melt Where This Cement Will Stand." pic.twitter.com/PPhsDsqqoF
— Mavis Nye Dr (hon) BEM. BCAh (@Grandmamavis) March 7, 2018
In summary, furnace cement is a versatile cement that is easy to use and relatively inexpensive. However, it is not as durable as other high-temperature cements and is not suitable for use in all applications.
What is Refractory Cement?
Refractory cement is a type of cement that is designed to withstand even higher temperatures than furnace cement, typically up to 5000°F. It is composed of materials such as alumina, silica, and fire clay, which are mixed with water to form a paste-like consistency. Refractory cement is used in a variety of applications, including lining furnaces, kilns, and fireplaces.
One of the primary advantages of refractory cement is its durability. It can withstand extreme temperatures and is resistant to cracking and breaking down over time. Refractory cement is also suitable for use in applications where it will be exposed to direct flame or extreme temperatures.
However, refractory cement also has its disadvantages. It is more difficult to work with than furnace cement and requires specialised equipment and knowledge to apply correctly. Refractory cement is also more expensive than furnace cement, making it a less popular choice for DIY projects.
Some common brands of refractory cement include MEECO'S RED DEVIL Refractory Cement, Rutland Castable Refractory Cement, and Kast-O-Lite 30 LI Plus Castable Refractory.
In summary, refractory cement is a durable cement that can withstand extreme temperatures and is suitable for use in a variety of high-temperature applications. However, it is more difficult to work with and more expensive than furnace cement, making it a less popular choice for DIY projects.
Differences between Furnace Cement and Refractory Cement
While both furnace cement and refractory cement are designed to withstand high temperatures, they differ in composition, temperature resistance, durability, and application methods.
Composition: Furnace cement is typically composed of materials such as silica, alumina, and calcium aluminate, while refractory cement is composed of materials such as alumina, silica, and fire clay. Refractory cement also contains a higher percentage of alumina, which gives it its high-temperature resistance.
Temperature Resistance: Furnace cement can typically withstand temperatures up to 3000°F, while refractory cement can withstand temperatures up to 5000°F. This makes refractory cement a better choice for applications where extremely high temperatures are present.
Durability: Refractory cement is more durable than furnace cement and can withstand extreme temperatures without cracking or breaking down. Furnace cement, on the other hand, is less durable and can crack and break down over time due to exposure to heat and moisture.
Application Methods: Furnace cement is easier to work with than refractory cement and can be applied with a trowel or putty knife. Refractory cement, however, requires specialised equipment and knowledge to apply correctly, such as a pneumatic gun or a casting mold.
In summary, the main differences between furnace cement and refractory cement are their composition, temperature resistance, durability, and application methods. Refractory cement is more durable and can withstand higher temperatures than furnace cement, but it is also more difficult to work with and more expensive.
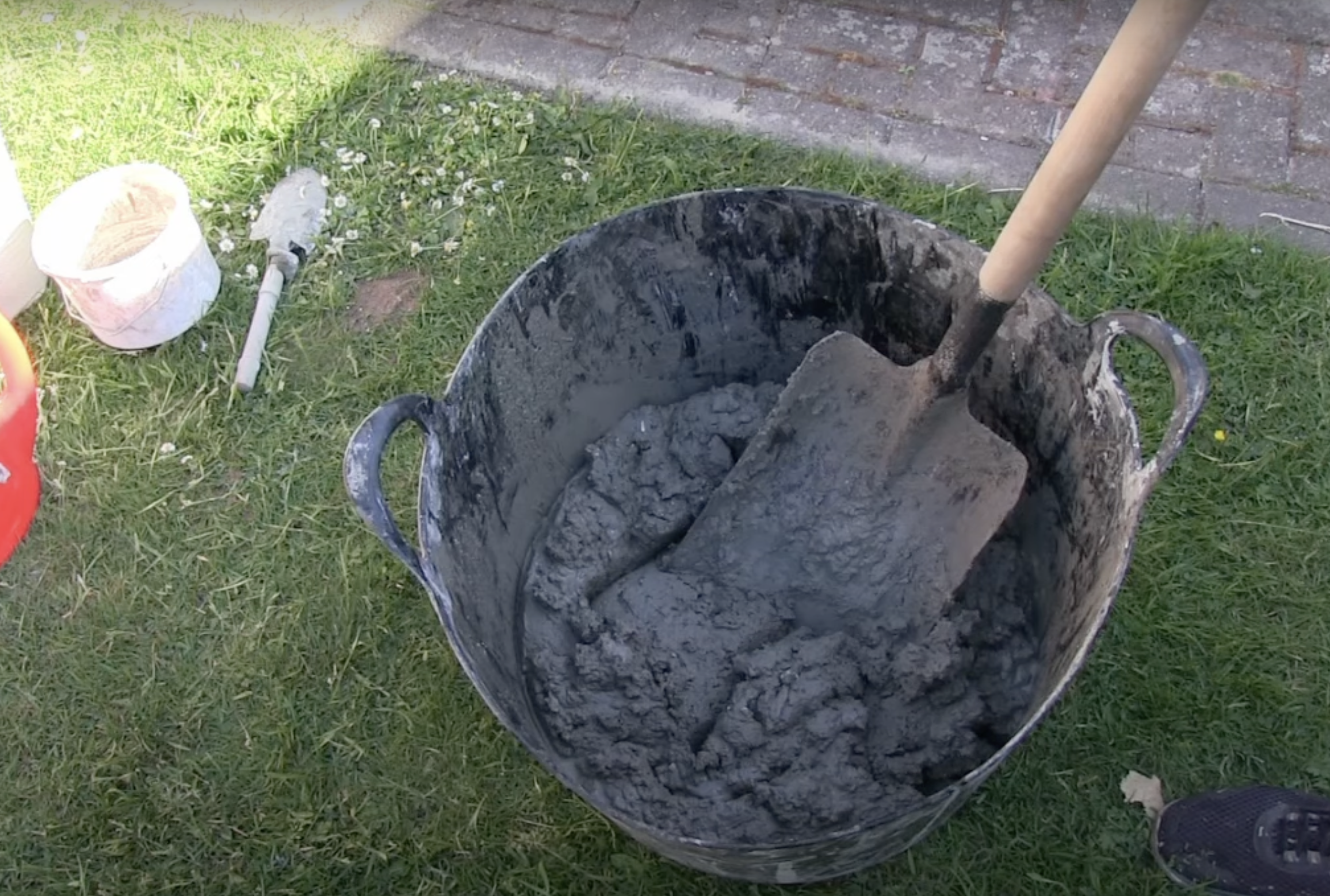
Choosing the Right Cement for Your Project
When choosing between furnace cement and refractory cement, there are several factors to consider (If neither is easier available or suitable for your application then maybe Fire Bricks are a good option for you? )
Temperature: The first factor to consider is the temperature of the application. If the application will be exposed to temperatures over 3000°F, refractory cement is the better choice. If the application will be exposed to temperatures below 3000°F, furnace cement may be sufficient.
Durability: The second factor to consider is the durability of the cement. If the application requires a cement that will withstand extreme temperatures and last for a long time, refractory cement is the better choice. If the application is not as demanding and a less durable cement will suffice, furnace cement may be sufficient.
Application: The third factor to consider is the application method. If you are a DIYer and do not have specialised equipment or knowledge, furnace cement is the better choice. If you have access to specialised equipment and knowledge, refractory cement may be an option (but not completely necessary as Gary below has shown us it can be done).
I cast refractory cement for the first time and it was not a disaster! now I have a lid https://t.co/44EnzsCJqm pic.twitter.com/ph5Z4xjWr5
— Gary Olsen (LosHuertos) (@garylosh) October 23, 2021
Cost: The final factor to consider is the cost. Furnace cement is typically less expensive than refractory cement, making it a more popular choice for DIY projects. Refractory cement, on the other hand, is more expensive but may be worth the investment for applications that require high durability and temperature resistance.
In summary, when choosing the right cement for your project, consider the temperature, durability, application method, and cost. It is important to choose the right cement for your application to ensure that it will withstand the demands of the environment and last for a long time.
Conclusion
In conclusion, furnace cement and refractory cement are two essential materials used in high-temperature applications. While both cements are designed to withstand high temperatures, they differ in composition, temperature resistance, durability, and application methods.
Furnace cement is a versatile cement that is easy to use and relatively inexpensive. However, it is not as durable as other high-temperature cements and is not suitable for use in all applications. Refractory cement, on the other hand, is a durable cement that can withstand extreme temperatures and is suitable for use in a variety of high-temperature applications. However, it is more difficult to work with and more expensive than furnace cement.
When choosing the right cement for your project, consider the temperature, durability, application method, and cost. It is important to choose the right cement for your application to ensure that it will withstand the demands of the environment and last for a long time.
Some common brands of furnace cement include Rutland Furnace Cement, Quikrete Furnace Cement, and DAP High Heat Mortar. Some common brands of refractory cement include MEECO'S RED DEVIL Refractory Cement, Rutland Castable Refractory Cement, and Kast-O-Lite 30 LI Plus Castable Refractory.
In summary, understanding the differences between furnace cement and refractory cement is crucial when choosing the right material for your project. By considering the temperature, durability, application method, and cost, you can make an informed decision and ensure that your high-temperature project is a success.