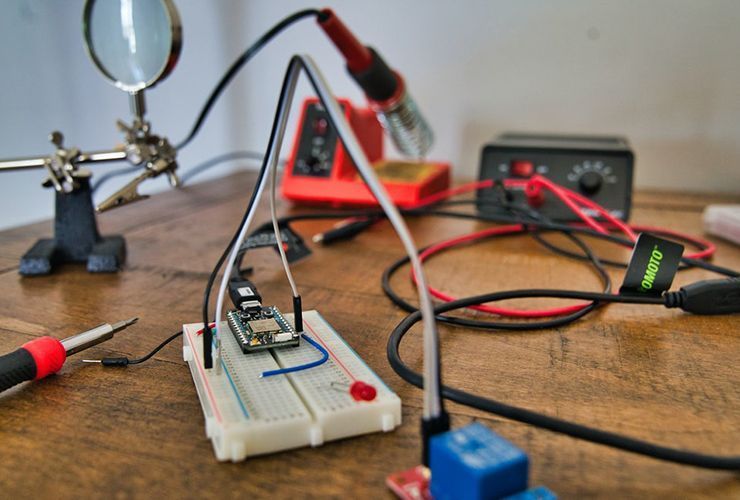
What Soldering Iron/Station do I need?
It is a challenge choosing the right soldering station, not only for the newbies but also the experienced professionals.
Today’s electronic equipment has really advanced, and is advancing every year, with ever increasing complexity, while a decreasing in dimensions and weight.
This has resulted in difficulty in the assembly of parts during the manufacturing process and also during repair and maintenance.
Soldering stations are employed in the making of conductive joints between electrical boards, electrical components or electrical wires.
They are employed in many professional industries as well as with hobbyists such as remote controlled vehicle enthusiasts or beginner radio operators.
Although fusing of PCB component is carried out by machines, repair works are carried out by humans.
The success of repair work depends on the skill of the expert employed and the kind of fusing station used. The soldering iron has become a tool used in many households, leading to the production of a wide variety of dedicated soldering stations that can repair almost any device available today.
Choosing the Right Soldering Station?
Choosing the right soldering station makes the difference between functional, superb connections and ugly, useless mess. It is recommended you do some research before choosing the right soldering station for your work, so as to find one that is quality, fits into your work needs and meets your budget.
But first decide the purpose you are going to be using the station for and the type of materials and connections you will be soldering. It is very important that you consider this as it decides the power (wattage) of soldering station you will need and whether you will need one with a variable temperature control.
Remember that a higher wattage does not translate to a higher temperature. All it means is the station will heat faster so it will be able to cater for the rapid loss of heat experienced during soldering of components with large motherboards or fusing of wires.
Also note that delicate boards will need lower temperatures with more precise temperature control. Therefore, in this case, an adjustable temperature fusing station would be ideal.
For smaller fusing projects such as circuit boards, wattage of 15 to 30 would be appropriate, but for larger fusing projects, power of 40 would be appropriate.We are going to look at the different characteristics of welding stations to help you make the right choice when choosing one. We are going to look at their functional characteristics and application methods.
Soldering stations are divided into the following categories:
- Lead-free contact
- Contact
- Infrared
- Desoldering
- Hot air
- Combined hot air
Contact Soldering Station:
The most commonly used and popular ones are the contact soldering stations. They differ slightly from traditional welding irons, but they lack the same design deficiencies.
The most common problem found in welding irons is the overheating of the sensor element, more so the semiconductor ones as they lack heater temperature adjustment.
As the soldering iron heats up to about 400 degrees, safety of the solder is ensured with short-term contact between the solder alloy and the soldering iron tip.But with contact soldering station, galvanic separation between the power circuit and the heating element is ensured by the inbuilt power supply unit.
And the voltage in the heating element can be adjusted from the power supply unit, changing the heating temperature accordingly. Typical optimal soldering temperature ranges from 250-330oC.
Examples of common models of contact soldering stations include the Lukey 936+, the AOYUE 936, and the AOYUE 937+.
Welding stations have heat stabilization units achieved with the aid of PID controls with back-coupling using tip temperature.
When the tip touches the solder alloy, the microcontroller examines the interrelation between the set temperature and the real temperature so that it automatically stabilize it when there is increase in voltage on the heating element.
Ordinary welding stations have power not exceeding 50-60 Watt, even putting into account the heat stabilization unit.
They may be employed for welding with lead non-refractory welding alloys. They are typically used by service experts for fixing contemporary RoHS PCBs with the use of headstrong lead-free soldering alloys.
But the downside of this is the following:
- Lifetime reduction with overheating of the soldering tip
- Low quality welding (cold soldering)
- Increased welding temperature leads to overheating of the radio component.
- Heating element operation time significantly decreases
- PCB track overheats
Lead-Free Soldering Station:
To do away with these problems, lead-free soldering stations are employed for fixing contemporary electronic or electrical equipment. They are similar to conventional welding stations in their operation principal, but with a heating power element from 75-80 Watt up to 150-160 Watt.
Their microcontroller has enhanced functionality to minimize the time it takes for temperature to stabilize. More advanced PID controls are used for this purpose.Examples of lead-free soldering stations are the Goot PX-501, the Goot RX-802AS, the AOYUE 2900, the ATTEN AT80D, and the Goot RX-852AS.
The Goot PX-201 seems to be a welding iron but is in fact a fully operational lead-free soldering station in a compact design.
Note that you can use lead solders in lead-free soldering stations as they are compatible no less than in case of ordinary contact stations.
Not all fusing work can be accomplished using contact soldering, for example, work involving Surface-mount technology (SMT) equipment, meaning dealing with leadless BGA chips and miniature SMD-components.
It is not only difficult using the fusing iron to do such work but in most cases simply impossible. Now, this is where non-contact soldering stations come in. They were designed for such tasks. Most common ones are the hot air soldering stations.
Operating Principal behind a Hot Air Soldering Station:
The mechanism behind the operation of hot air soldering station is rather simple. This is how it works—air flow is created by a compressor, heating up to a certain temperature while moving through the heating spiral element.
The air flow getting out of the heat gun is directed into the fusing area. This offers solution to the problem of fusing in congested space where several contact packs are heated.
Hot air soldering stations are widely used for the repair of mobile phones and household appliances.
They have enough power for operation with lead and lead-free fusing alloys though their application use is restricted. However, hot air soldering stations cannot be used for large BGA chips soldering or desoldering. Examples of hot air soldering stations include the ATTEN AT860D, the Lukey 850D, the AOYUE 857A++, and the Pro’sKit SS-601F.
Hot air soldering stations became popular as they could be used in combination with other welding equipment types. For example, a hot air gun could be combined with a soldering iron.
Choosing the Right Soldering Iron
A soldering iron is a handheld tool used in electronics and circuit board soldering and de-soldering. Many soldering irons are available on the market coming in different sizes and shapes.
But choosing the right soldering iron is what makes the different on the job you are doing. And choosing a certain soldering iron depends on the job you are planning to do as well as how frequent you are planning to use it.
One of the most common concern for people doing soldering jobs in electronic applications is the concern of choosing the right soldering iron ideal for electronics and circuit board work. Most soldering jobs involve joining small parts thus high precision is required.
When a solder is overheated, it can mess up the element being worked on even mess up the whole component work. Soldering jobs are handled by technicians as well as laypersons thus the soldering iron needs to be of really high standards. This raises the question of how to choose the best soldering iron and what kind of wattage is needed and the features the soldering iron have being used on the job should have.
Let us look at electronic soldering jobs that call for use of heavy soldering. This jobs can range from devices such as televisions, radios, PCBs and many others. A student may be assembling a radio using an assembly chart provided to him as part of his course assignment.
The student needs to mount several electronic components on to the PCB by soldering them using a soldering iron with the aid of flux. Things that need soldering include resistors, ICs, diodes, small wires and capacitors.
Even just a small mistake when soldering these elements can result to damage to the component being soldered, including the PCB track, which would be more serious.
Of course good soldering is achieved with the right skill and experience but ultimately with the aid of a good soldering iron. Therefore it becomes inevitable that one should use a good soldering iron.
What to Look For When Choosing the Right Soldering Iron?
Wattage:
This is one of the most important factor to consider when choosing a soldering iron.Chose a solder iron that has wattage of between 20 Watts to 60 Watts or 15 Watts to 40 Watts.
You can go for a 40 Watt soldering iron, which you can regulate the range of wattage between 15 Watts to 40 Watts thus would be able to control its temperature. Other soldering irons are in the range 20 Watt to 60 Watt.
One with 50 Watt is also commonly used and it provides enough heat for most soldering jobs on the circuit boards. Generally, those with higher wattage are better. Remember it doesn’t mean that soldering irons with higher wattage supply more heat to the solder joint; it just means it has more power available.
You can control amount of the heat on the iron tip using the power station knob. Soldering iron with low wattage can lose heat faster than it can re-heat itself.
Weight:
Electronic jobs often involve working with delicate components thus choose a soldering iron that is slim and light weight and provides for a good handling through its grip.
Supports Multiple Solder TipsDelivering the right amount of heat to the component being worked on calls for use of the right size of solder tip. Therefore, choose a solder iron that provides provision for replacing solder tip with another different one according to your work needs at the moment.
Type of Soldering Iron
There are many types of soldering irons. Soldering irons with basic pencil style irons are suitable for hobbiest use but go for one that can heat the joints quickly enough. Adjustable temperature iron gives you control and allows you to work faster and flexible.
But a joy to work with is a temperature-controlled iron with interchangeable tips and 50 watts or more of power. It has feedback control that keeps the iron tip temperature at a precise needed level and a watts speed recovery time feature to allow you work faster.
Butane powered irons have much power but are difficult to control and battery powered irons are generally underpowered for most works.
But first consider what is your purpose for choosing the soldering iron for your job. Are you a skilled professional who is doing a high end job or you just want a soldering iron for a hobby project.