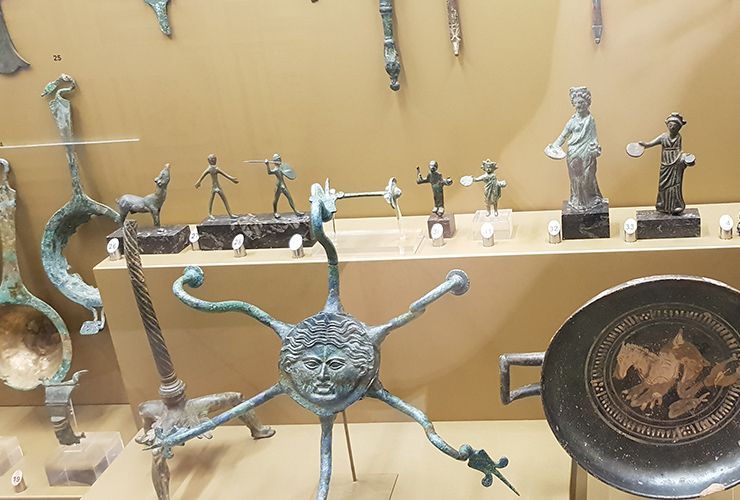
Bronze casting (history)
A brief history of bronze and lost wax casting
During the third millennium B.C., ancient Greek artisans experimented with beeswax carvings and discovered that bronze had distinct advantages over copper in the creation of statues. Bronze is an alloy of 90 percent copper and ten percent tin. It has a lower melting point than copper, remains in a liquid state longer than copper when filling molds, and it also produces a better quality casting than pure copper with a superior tensile strength. The melting point of bronze is approximately 9500C (1,7420F) and copper’s melting point is 1,0850C (1,9840F).
Greeks and Romans have an extended history in the creation of bronze sculpture. Thousands of images of gods and heroes, as well as acclaimed athletes and philosophers, filled the temples and public spaces in Greece and Rome. There were many sources of copper around the Mediterranean to supply these artisans, but the island of Cyprus, whose name derives from the Greek word copper, was their mainstay. Tin was imported from places as far as Turkey, Afghanistan, and England.
The earliest large-scale Greek bronze statues were produced with the simple and crude technique known as sphyrelaton (meaning hammer driven). Sphyrelata were created by hammering thin sheets of bronze around a core of wood previously carved to take the desired shape.
The technique appears to be of oriental origin, imported from north-Syrian workers arriving in Greece around the 17th century B.C. Significant sphyrelaton works were attributed to the mythical figure of Daedalus, as similar votives were discovered from excavations on the island of Crete. Sphyrelaton went out of use around 500 – 480 B.C. and was replaced with lost-wax casting as the major technique used in the production of bronze statuary.
Lost Wax Casting
Solid lost-wax casting, which is the earliest and simplest process, uses a solid wax model. The model is wrapped in clay, then heated to remove the wax and harden the clay. The model is turned upside down and molten bronze is poured into it. When the metal cools, the clay is broken to reveal the solid bronze sculpture. Other forms of lost-wax casting include hollow lost-wax casting by the direct process and hollow lost-wax casting by the indirect process.
With the hollow lost-wax casting by the direct process, the sculptor is able to produce larger works cast in several pieces, i.e. the head, body, arms, and legs. The framework made of iron rods is used to secure the model’s core. This core is then coated with wax, with ventilation added to support easy flow of molten metal, and to allow gases to escape to ensure a uniform casting. The model is then coated with a layer of clay, and heated to remove the wax. The mold is reheated again for a longer period of time to remove any wax residue. Molten bronze is then poured into the mold until it’s full. When the bronze has completely cooled, the mold is broken and is ready for finishing.
For hollow lost-wax casting by the indirect process, the wax model is not lost in the casting process. This allows for replication of the same model in part and whole, and to cast large-scale statues in sections. Because of the advantage offered by the indirect process, Greeks and Romans used this method of casting to produce large-scale statues.
The initial model is usually made of clay or plaster. A mold is then made around the model to duplicate its form. The mold is then cut into sections without undercutting the model. After drying, the model pieces are secured together with a thin layer of beeswax. The artist assesses the form for authenticity in the molds details. He/she makes corrections as needed. Funnels, channels, and vents are attached to the model before being covered with layers of clay.
The mold is heated twice and during the second heating, molten bronze is poured into the mold. After cooling, each mold section is broken open to reveal each section of the bronze statue. The sections are then cleaned up with abrasives. All pieces are then joined together through welding or mechanical means. The sculptor adds on decorative touches through chiseling, hammering, inlays of other metals, and stonework. These fine details are why the Greeks and Romans are so famously known for their precision craftsmanship and this art form is still used today by artists all over the world.